All You Need to Know About PVD Stainless Steel
PVD (Physical Vapor Deposition) coating technology has gained significant attention in recent years, especially in the stainless steel industry. This technique not only enhances the aesthetic appeal of stainless steel but also improves its durability. Let’s dive into the fascinating world of PVD coated stainless steel!




What is PVD Finish on Stainless Steel?
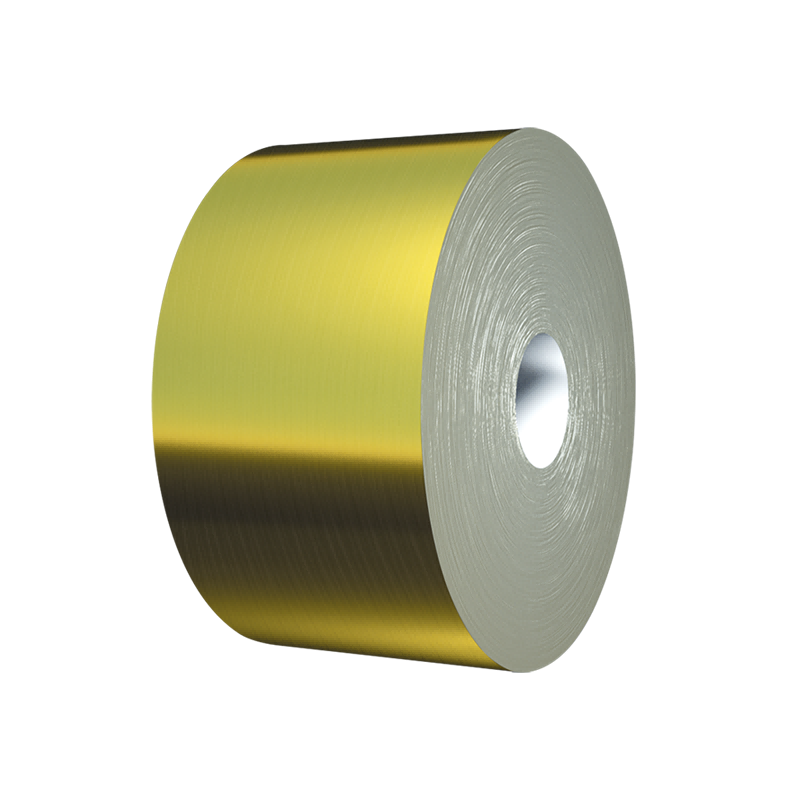
PVD coating involves applying a thin, hard film to the surface of stainless steel through a physical process. This film significantly enhances the material's properties and creates various color options, such as gold, rose gold, black, and bronze. The coating materials, often metals like titanium and aluminum or ceramics, are vaporized in a high-temperature, low-pressure environment and deposited on the stainless steel surface.
For our PVD stainless steel coils, we use vacuum PVD coating technology. This process avoids chemical liquids, like dyes or electrolytes, achieving a flawless and consistent coating across entire coils without color discrepancies.
Difference Between Raw Stainless Steel and PVD-Coated Surfaces
Imagine raw mill-finished stainless steel as a “plain” version with a silver-gray, smooth surface like a 2B finish. While practical, it is prone to fingerprints, dirt, and oxidation over time. PVD-coated stainless steel transforms into a “polished gentleman,” boasting enhanced scratch, corrosion, and oxidation resistance, along with a striking appearance.
PVD Coating Process for Stainless Steel

The PVD coating for stainless steel involves three main steps:
- Vacuum Heating: Stainless steel is placed in a vacuum chamber and heated to vaporize the coating material.
- Ionization: The material vapor is ionized using an electric or magnetic field.
- Deposition: These ions bond firmly to the stainless steel surface, forming a robust film.
Our PVD coating stainless steel sheets production process ensures precision through parameter control, allowing accurate color adjustment. After coating, advanced instruments measure and quantify color values to meet customer expectations.
The specific operations can be viewed in the following video, which will take you through the entire process of PVD coating on stainless steel.
The Thickness Range and Hardness of PVD Coatings

PVD stainless steel coating are thin (0.1-3 μm), maintaining the base material's mechanical properties. With hardness levels of HV800-3000, they offer exceptional wear resistance. For decorative coatings, thickness typically ranges from 0.1-1 μm, preserving the original dimensions of the material while enhancing surface properties.
PVD Coating Advantages and Disadvantages

Advantages of PVD Coating
PVD coating offers several significant advantages, especially when compared to electroplating:
- Hardness and Wear Resistance: PVD-coated stainless steel can reach hardness levels up to HV3000, effectively withstanding high-friction environments, while electroplated coatings typically have lower hardness and wear resistance.
- Diverse Colors and Decoration: PVD coatings are available in various colors, including gold, rose gold, black, and blue, making them suitable for multiple industries like fashion, architecture, and automotive. In contrast, electroplated finishes' color choices and consistency may be harder to guarantee in mass production.
- Corrosion Resistance: PVD coatings are chemically stable and can maintain excellent performance even in harsh environments, whereas electroplated coatings may be more susceptible to corrosion in certain chemical conditions.
- Thickness Advantage: PVD coatings typically range from 0.1 to 3 micrometers thick. While this is relatively thin, their performance is significantly strong. In contrast, electroplated coatings can be thicker, but excessive thickness may lead to reduced adhesion and impact durability.
- Eco-Friendly: PVD coatings are free from harmful solvents, making them a sustainable surface treatment option. In comparison, the electroplating process may involve hazardous chemicals, posing an environmental burden.
Potential Limitations of PVD Coating
- Color Variation: In large-scale production, particularly in the manufacturing of PVD-coated stainless steel sheets, it may be challenging to ensure color consistency across the surface.
- Thickness Limitations: The coating is typically thin (0.1-3 μm), which may not meet the needs of applications requiring a thicker protective layer.
- Coating Delamination: Ordinary PVD coatings can experience delamination due to internal stresses, improper surface treatment, and ongoing exposure to external impacts and friction. Under normal indoor conditions, the typical lifespan is around 5-10 years.
PVD Coating Stainless Steel Coil – The Key to Uniform Color
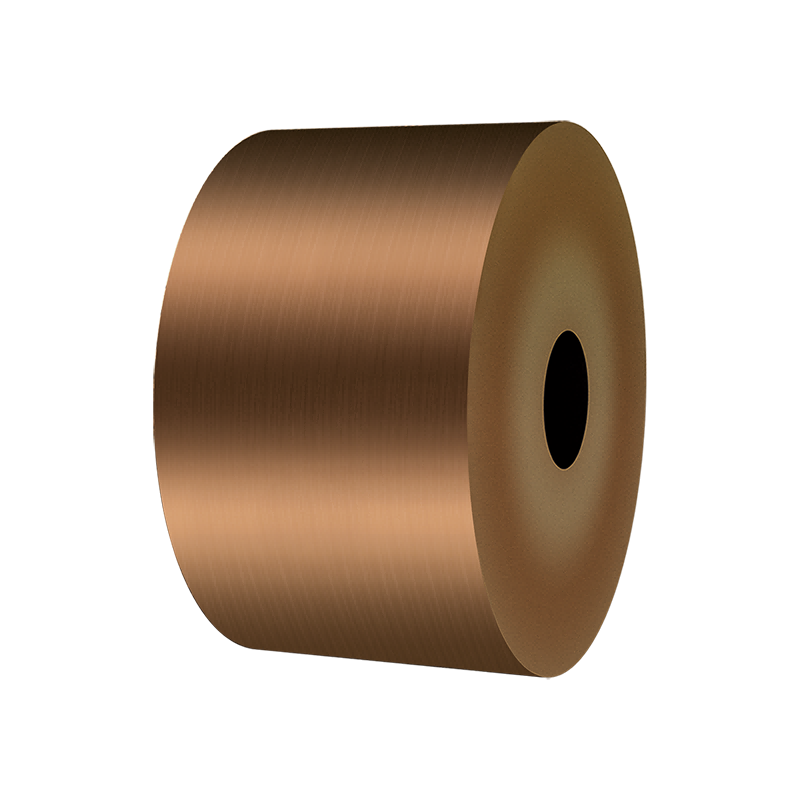
China pioneered coil PVD stainless steel coating technology in 2020, resolving issues like low yield and inconsistent colors. Advanced German technology further enhances this process, offering:
- Consistent Color: Ensures uniform color across and between batches, perfect for large decorative surfaces.
- Flexible Cutting: Designers can cut custom sizes from the coil, avoiding mismatched sections.
- Cost Efficiency: Higher production efficiency, shorter lead times, and lower costs make it ideal for large-scale projects.
In addition, our stainless steel coil has a surface wear resistance of up to 1000 cycles per 10N (the general industrial standard is 500 cycles per 10N). This level of surface wear resistance is industrial-grade, surpassing and setting a new standard in the Chinese industry, alleviating your concerns about PVD coating delamination on stainless steel.
Do you also desire to solve these problems? Our PVD coated stainless steel coil can help you.
Uses for PVD Coated Stainless Steel

PVD coating stainless steel excels in various industries:
- Architecture: Facades, interiors, windows, countertops.
- Transportation: Automotive emblems, trims, and aviation components.
- Jewelry: Stunning colored and textured accessories.
- Electronics: Smartphone casings and electronic components.
- Automotive Parts: Enhancing vehicle aesthetics and durability.
How to Maintain PVD Coated Stainless Steel

Cleaning
To maintain the pristine look of your PVD-coated stainless steel, follow these scientific cleaning methods:
- Use mild soap and water: Mix a small amount of mild, pH-neutral soap with warm water. Dip a soft microfiber cloth or sponge into the solution and gently clean the surface.
- Avoid abrasives: Never use steel wool, abrasive pads, or harsh cleaning agents, as these can scratch or damage the PVD coating.
- Rinse thoroughly: After cleaning, rinse the surface with clean water to remove any soap residue that might dull the finish.
- Dry immediately: Use a dry, soft microfiber cloth to gently pat the surface dry. This step prevents water spots or streaks from forming.
- Periodic maintenance: Use a non-abrasive stainless steel cleaner specifically designed for coated surfaces for periodic deep cleaning. Follow the manufacturer’s instructions for best results.
Removing PVD Coating
Firstly, we strongly advise against removing the PVD coating yourself!
Here’s why:
- Surface damage: DIY removal risks damaging the underlying stainless steel, impacting its aesthetic appeal and reducing corrosion resistance.
- Accelerated oxidation: Without the protective PVD layer, the stainless steel may react with environmental factors, hastening oxidation and corrosion.
If you’re tired of your current design, we recommend contacting us to custom-create a new style for you—efficient, hassle-free, and tailored to your needs.
Still insistent on DIY? Here are some basic suggestions:
- Chemical methods: Use a paint or coating remover compatible with stainless steel. Carefully apply the remover with a soft brush, ensuring you follow the product’s instructions to avoid etching or pitting the metal.
- Mechanical methods: Sandblasting or using fine abrasive pads can physically strip the PVD layer, but this should only be attempted with the proper equipment and protective measures.
- Test in a small area first: Always test your chosen method on a hidden or inconspicuous area to ensure it doesn’t irreparably damage the surface.
⚠️ Warning: Proceeding with DIY removal is at your own risk. Contacting professionals for assistance is always the safer and more effective choice.
Scratch Resistance
While PVD coatings offer high hardness and resistance to scratches, they are not completely immune to damage. Here’s how to minimize risks:
- Handle with care: Avoid placing sharp or abrasive objects directly on the surface. Use protective mats or pads when necessary.
- Clean appropriately: Follow the cleaning methods outlined above to avoid introducing fine scratches during maintenance.
- Apply protective films: For high-traffic or heavily-used areas, consider applying a transparent protective film to safeguard the PVD coating from wear and tear.
- Polish minor scratches: For superficial scratches, use a non-abrasive polish recommended for stainless steel. Apply gently with a soft cloth to restore the surface’s shine.
By following these steps, you can extend the life and beauty of your PVD-coated stainless steel while minimizing potential damage.
Future Trends

According to research, the future of PVD coated stainless steel technology focuses on sustainability, meeting strict environmental standards while catering to growing demands. Innovations will enhance uniformity, adhesion, and efficiency, with expanding applications in emerging fields like electric vehicles (EVs), consumer electronics, and aerospace. Automation and digitization will drive consistency and productivity, positioning manufacturers for global competitiveness.
Discover the endless possibilities of PVD-coated stainless steel for your next project!
Surface finishing technologies have continuously evolved to meet the growing demand for patterns and colors on stainless steel. Beyond plain-colored stainless steel sheets, PVD-coated techniques can combine with brushing, etching, embossing, and 3D engraving to create designs that cater to a variety of high-end decorative needs.
At Sanmei Metal, we keep pace with the times by offering beautiful yet practical stainless steel sheets based on 201, 304, and 430 grades. Our stainless steel coils can also be enhanced with mirror, brushed, or other effects on top of your favorite PVD colors. Tempted? Don’t wait—take action now!




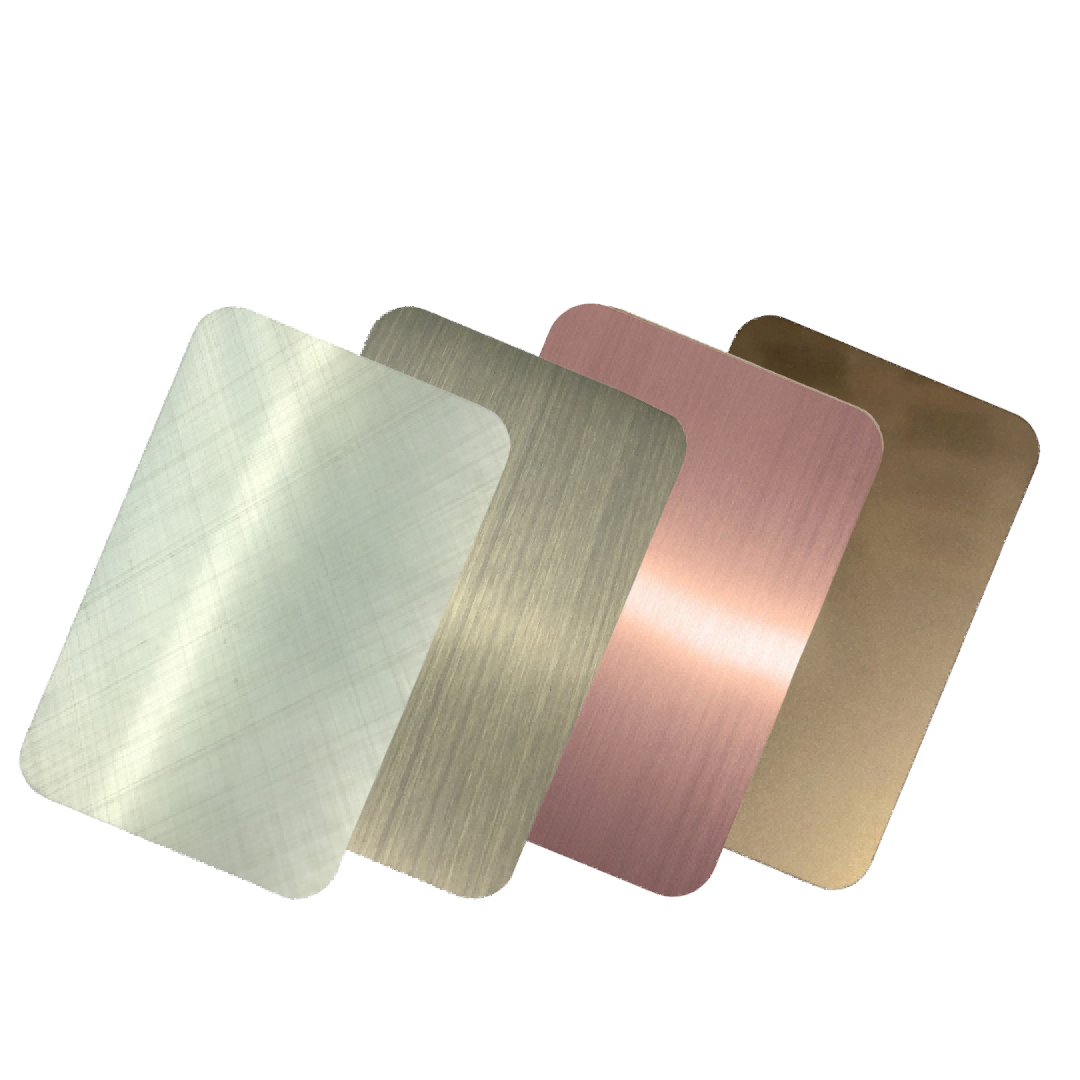



hello.
to remove PVD from stainless steel - a sulfuric acid bath will work?
70Ma for 5-10 minutes?
Thanks for reaching out! We mainly focus on supplying PVD stainless steel, so we’re not experts in PVD removal, but we’ve checked with some industry peers about your question.
A sulfuric acid bath can work to remove PVD coatings, and your idea of using 70mA for 5-10 minutes seems like an electrochemical stripping method. However, how well it works depends on the coating type and thickness. Here are a few things to keep in mind:
Acid Concentration: Usually, a 10-30% sulfuric acid solution is used. Be careful, though, higher concentrations might damage the stainless steel.
Temperature: A heated bath (50-70°C) can speed up the process, but it needs to be handled with care.
Alternative Methods: If the coating’s tough (like TiN or ZrN), you might need a hydrofluoric acid mixture or a high-alkaline solution.
Since effectiveness can vary, it’s best to test on a sample before going for a larger batch. Let us know if you need more help!